The Many Faces of Kilns: From Glass to Blades
Kilns have been essential tools for thousands of years, playing a crucial role in transforming raw materials into durable, functional, and artistic creations. While most people associate kilns with pottery and ceramics, their applications extend far beyond that. From glasswork and metal processing to culinary arts and industrial manufacturing, kilns are indispensable in numerous fields.
In this article, we’ll dive deep into the diverse world of kilns, exploring their role in pottery, glass fusing, knife making, enameling, cement production, and even culinary applications.
The Heart of Pottery: How Kilns Bring Clay to Lif
At the core of pottery and ceramics lies the kiln—a powerful tool that hardens and strengthens clay through a carefully controlled firing process. This transformation is what turns delicate, malleable clay into solid, durable ceramic pieces that last for centuries.
The Science of Ceramic Firing
The magic of pottery firing happens in three key stages:
- Drying Phase: Before firing, clay must be thoroughly dried to remove all moisture. Any remaining water can cause cracking or even explosions in the kiln.
- Bisque Firing: The first firing stage, usually between 1,800−2,000°F (982−1,093°C), hardens the clay but leaves it porous enough to absorb glaze.
- Glaze Firing: A second firing, often at higher temperatures (up to 2,400°F / 1,315°C), melts the glaze, creating a smooth, glassy surface.
The kiln does more than just harden clay—it activates chemical reactions that determine the final color, texture, and strength of the piece.
Types of Ceramic Kilns
- Electric Kilns: Common in studios and schools, offering precise temperature control.
- Gas Kilns: Used for high-fire pottery, allowing for oxidation and reduction effects.
- Wood-Fired Kilns: Traditional and unpredictable, producing unique, organic glaze finishes.
- Raku Kilns: Specialized for rapid cooling, creating crackled glaze effects.
Glass Kilns: The Art of Fusing and Slumping
Kilns are just as vital in the world of glasswork, where they are used for fusing, slumping, and annealing glass into stunning shapes and designs.
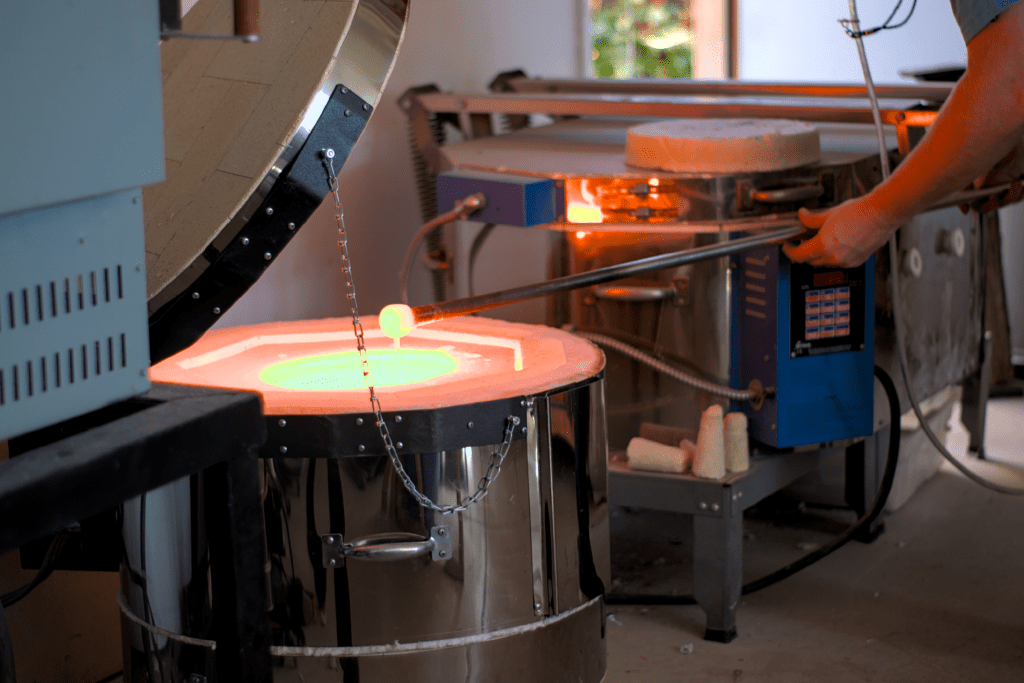
Fusing: Merging Glass Layers
Glass fusing involves stacking different pieces of glass and heating them until they bond together. This process occurs at temperatures ranging from 1,099 to 1,501°F (593−816°C). Artists use fusing to create layered designs, intricate patterns, and even three-dimensional objects.
Slumping: Molding Glass into Forms
In slumping, the kiln heats the glass just enough to allow it to slowly «slump» over or into a mold, taking on a new shape. This technique is commonly used to make bowls, plates, and decorative sculptures.
Unlike pottery, glass kilns require careful temperature control to prevent cracking from thermal shock.
Annealing: Strengthening Glass for Durability
After shaping, glass must be gradually cooled in a process called annealing. This relieves internal stress and prevents the glass from shattering over time. Kilns designed for annealing allow for slow, controlled cooling, ensuring a strong and stable final product.
Knife Making: How Kilns Forge Stronger Blades
In the world of knife making, kilns play a vital role in heat treating, a process that strengthens metal blades by altering their molecular structure.
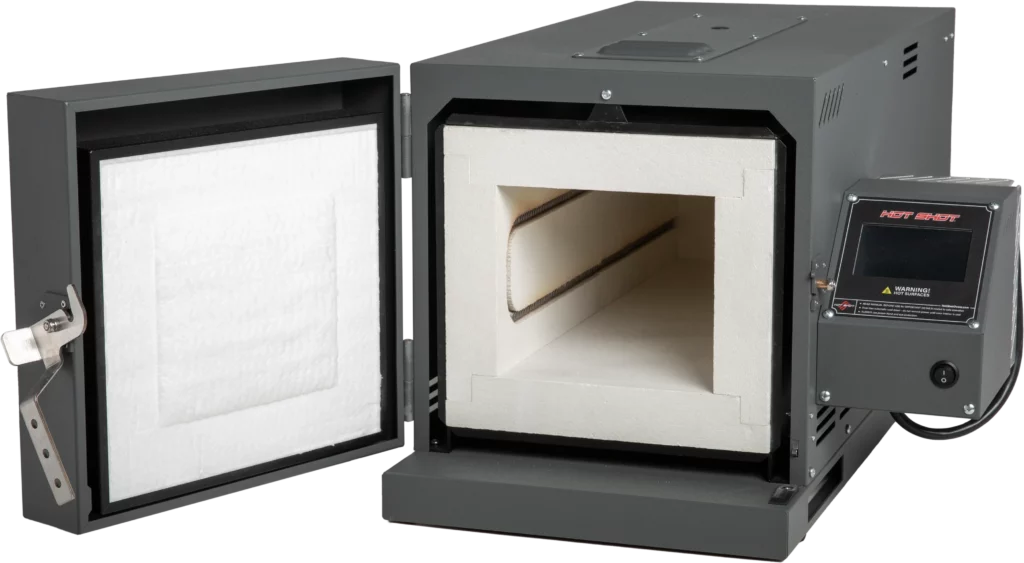
The Heat-Treating Process
- Hardening: The blade is heated to high temperatures (up to 2,200°F / 1,204°C) and then rapidly cooled (quenched) to lock in a hardened state.
- Tempering: To reduce brittleness, the blade is reheated at a lower temperature, making it tougher and more resilient.
Without controlled kiln temperatures, a blade could become too brittle, too soft, or prone to breaking.
Modern Kilns for Knife Making
Advanced knife-making kilns feature programmable controllers, allowing artisans to fine-tune the heat treatment process with incredible precision. Whether crafting a kitchen knife, hunting blade, or a collector’s piece, the kiln ensures a balance of hardness and flexibility.
Enameling: Creating Vibrant Designs on Metal and Ceramics
Enameling is an ancient technique where powdered glass is fused onto a surface—usually metal or ceramic—using high temperatures. The result is a glossy, colorful, and highly durable coating.
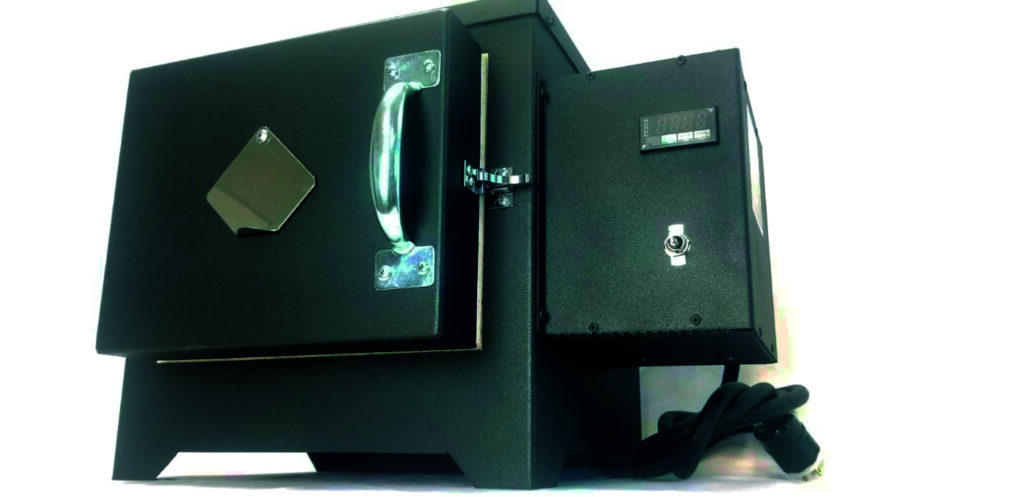
Different Enameling Methods
- Cloisonné: Metal wires create compartments filled with enamel, producing intricate designs.
- Champlevé: Recessed areas are carved into metal and filled with enamel.
- Basse-Taille: Transparent enamel is applied over engraved metal for a glowing effect.
- Plique-à-Jour: Enamel is suspended between metal edges, creating a stained-glass effect.
Whether used in fine jewelry, decorative plates, or architectural details, enameling turns ordinary objects into lasting treasures.
Industrial Kilns: Cement Production and Beyond
Beyond art and craft, kilns are at the heart of industrial processes, including cement production.

How Kilns Make Cement
- Raw materials (limestone, clay, and sand) are mixed and heated to 2,640°F (1,450°C).
- The intense heat triggers a chemical reaction, forming clinker—the essential ingredient in cement.
- The clinker is cooled, ground into a fine powder, and mixed with gypsum to create cement.
Without kilns, modern construction would be impossible.
Other Industrial Applications
- Metal refining: Extracting and purifying metals.
- Chemical processing: Creating specialized industrial compounds.
- Electronics: Kiln-firing components for semiconductors.
Culinary Applications: Baking and Roasting with Kilns
Surprisingly, kilns are also used in food preparation—especially for artisanal baking and coffee roasting.
Kiln Baking: The Secret to Perfect Bread and Pizza
Kilns provide ultra-high temperatures, resulting in crispy crusts and even heat distribution. Traditional pizza ovens, inspired by kiln designs, allow for rapid baking that locks in moisture and flavor.
Roasting Coffee Beans
Some specialty coffee producers use kilns to precisely control bean temperature and roasting profiles, enhancing flavor complexity.
In the hands of a skilled artisan, a kiln can create not just art, but unforgettable flavors.
The Indispensable Role of Kilns
From shaping clay and fusing glass to forging metal and processing industrial materials, kilns are versatile, powerful, and essential. Whether in an artist’s studio or a massive factory, these high-heat chambers transform raw materials into durable, functional, and artistic creations.
Next time you admire a ceramic mug, a stained-glass window, or a chef’s knife, remember—the kiln is the unsung hero behind it all.