The Art of Minakari: A Five-Step Process
Persian enameling, or Minakari, is an intricate craft that transforms plain metal objects into vibrant, detailed artworks. The process requires a steady hand, careful planning, and a deep understanding of materials and techniques. While online tutorials can provide a basic introduction, nothing compares to learning from experienced artisans who have mastered this centuries-old art form.
The true essence of Minakari lies in its details—each fine line and color transition contributes to the final masterpiece.
This article takes you through the five essential steps of Persian enameling, explaining each stage in depth to provide a clear picture of the process.
Step 1: Preparing the Surface
The foundation of a flawless Persian enamel piece starts with careful preparation of the metal surface. Traditionally, copper is the preferred material due to its excellent compatibility with enamel. However, before any artistic work begins, the surface must be meticulously refined to ensure proper adhesion and a smooth final finish.
The process starts with sanding the entire piece to remove any irregularities, oxidation, or impurities. This step is crucial because even minor imperfections can cause flaws in the final enamel layer. The goal is to achieve a perfectly even surface that allows for uniform application of the base enamel.
A well-prepared surface is the key to a successful Minakari piece—any roughness or contamination can affect the adhesion of the enamel, leading to cracks or discoloration after firing.
Once the metal is properly sanded, it undergoes a thorough cleaning process. Any residual dust, oil, or moisture must be completely removed, often using specialized cleaning solutions or acids that prepare the surface for enameling.
After cleaning, a base coat of enamel, typically white, is applied. This base layer serves multiple purposes: it enhances the vibrancy of the final colors, provides a smooth painting surface, and ensures a durable bond between the metal and the decorative enamels. The application is done either by dipping the piece into a liquid enamel suspension or by carefully brushing on an even layer.
The piece is then placed into a kiln and fired at high temperatures, often exceeding 800 °C (1472°F). During this stage, the enamel fuses to the copper, creating a strong, glass-like coating. This firing process may need to be repeated multiple times, with each layer adding to the depth and durability of the final design.
The firing stage is where the transformation begins—the raw, powdered enamel melts and bonds with the metal, setting the stage for the intricate patterns and colors that define Persian enameling.
Once the base enamel is fully fused and the surface is smooth, the piece is ready for the next step: sketching the design.
Step 2: Outlining the Design
With the base enamel securely fused to the metal, the next crucial step in Persian enameling is outlining the design. This stage requires precision and a steady hand, as it forms the blueprint for the intricate patterns that will later be filled with vibrant enamel colors.
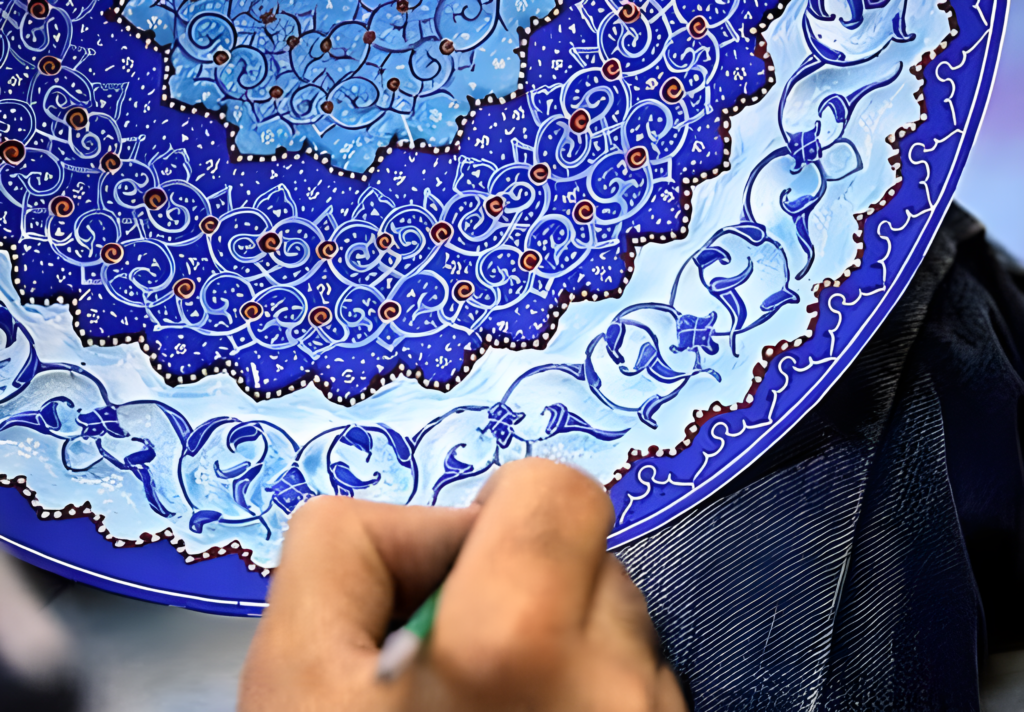
Artisans begin by transferring the design onto the surface of the enamel-coated piece. This can be done using various methods, depending on the complexity of the pattern. Some artists prefer freehand drawing, relying on years of practice to sketch elegant floral motifs or geometric designs directly onto the surface. Others use fine stencils or perforated templates, dusting charcoal or powdered pigment over them to create a faint yet accurate outline.
The balance and symmetry of the design are essential—any misalignment at this stage can affect the harmony of the final artwork.
Once the pattern is in place, it is reinforced using a special ink or fine brushwork to make the outlines more distinct. The ink used must be stable enough to remain visible throughout the enameling process but light enough to allow adjustments if necessary.
Traditional Persian Minakari designs often feature intricate arabesques, delicate floral patterns, or symmetrical motifs inspired by nature and Persian architecture. The artist carefully ensures that each section of the design is proportionate and well-spaced, as this will determine the overall aesthetic of the final piece.
A well-outlined design serves as a guide for the next stages, ensuring that each color and detail falls perfectly into place, preserving the beauty and integrity of the artwork.
Once the outline is complete, the piece is ready for the next step: applying the black pen to define and separate the sections of the design.
Step 3: Applying the Black Pen (Kontur Work)
With the design meticulously outlined, the next step in the Persian enameling process is applying the black pen, also known as «kontur work.» This stage is crucial for defining the details of the pattern and preventing the enamel colors from blending during the final firing.
A special black outlining mixture is used, consisting of finely ground graphite, glue, and other stabilizing agents. This mixture is carefully prepared to ensure the right consistency—too thick, and it will create raised, uneven lines; too thin, and it may bleed into the surrounding areas.
Using a fine-tipped applicator or a delicate brush, artisans carefully trace over the sketched design, reinforcing the contours and creating clear separations between different sections of the pattern. This step requires extreme precision, as the quality of the black outlines directly affects the final aesthetics of the piece.
The smoothness and uniformity of the black lines are key—any inconsistencies will become more noticeable once the vibrant enamels are applied.
One of the primary functions of the black pen is to act as a barrier during the glazing process. Since the enamel colors used in Minakari are in liquid or powdered form before firing, the black outlines help contain them, ensuring that each color remains within its designated section.
Once the black pen application is complete, the piece is left to dry thoroughly. This drying process is essential, as any premature handling can smudge or distort the carefully drawn lines. In some cases, a low-temperature firing is done at this stage to fix the kontur work in place before moving on to the next step.
Even though kontur work is one of the simplest steps in Minakari, it plays a major role in defining the final artwork. Perfectly executed black lines enhance the clarity, contrast, and depth of the design, making the colors stand out beautifully.
With the black outlines securely in place, the piece is now ready for the most colorful and exciting stage of the process—applying the enamel glazes.
Step 4: Adding Color with Enamel Glaze
With the black outlines firmly in place, the Persian enameling process enters its most vibrant and expressive stage—applying the enamel glaze. This is where the design comes to life, as rich and luminous colors fill the carefully defined sections of the pattern.
Traditional Minakari colors include deep blues, fiery reds, bright turquoises, and soft greens, each created from finely ground mineral pigments mixed with a binding agent. The choice of colors is not random; Persian enamel artists often follow time-honored color combinations that enhance the harmony and elegance of the piece.
The application process requires precision and patience. Using fine-tipped brushes or small pumps, artisans delicately place the liquid enamel into each section of the design, ensuring even coverage without spilling over the black outlines. The consistency of the enamel must be carefully controlled—too thick, and it may crack during firing; too thin, and it might not achieve the desired opacity.
The depth of color in Minakari is built layer by layer, with each firing intensifying the vibrancy and durability of the enamel.
Once the entire piece is glazed, it is left to dry before being placed in the kiln. The firing process, typically at temperatures around 800 °C (1472°F), fuses the enamel pigments with the base layer, creating a glossy, glass-like finish. Depending on the complexity of the design, multiple firings may be required, with additional layers of enamel applied between each round to refine the colors and enhance the final effect.
During firing, the true beauty of Persian enamel emerges—the heat transforms the dull, powdery pigments into brilliant, jewel-toned glazes, permanently bonding them to the metal surface. The artist must carefully monitor the kiln, as variations in temperature or firing time can alter the final shades or even damage the piece.
Mastering the art of glazing requires experience—controlling color flow, achieving smooth finishes, and balancing multiple firings to create depth and radiance in the enamel.
Once the colors are fully developed and the final firing is complete, the piece is carefully inspected for imperfections. Any necessary touch-ups are made before moving on to the last and most delicate phase of the process—polishing and final detailing.
Step 5: The Final Firing and Finishing Touches
After the vibrant enamel glazes have been carefully applied and fired, the Persian enameling process enters its last and most delicate stage—the final firing and finishing touches. This step ensures that the artwork achieves its characteristic brilliance, smoothness, and durability.
The final firing is crucial, as it sets the last layers of enamel and enhances the overall depth of color. The piece is placed in the kiln one last time, typically at temperatures exceeding 800 °C (1472°F). At this high heat, the enamel fully melts and fuses with the metal base, creating a glossy, glass-like surface.
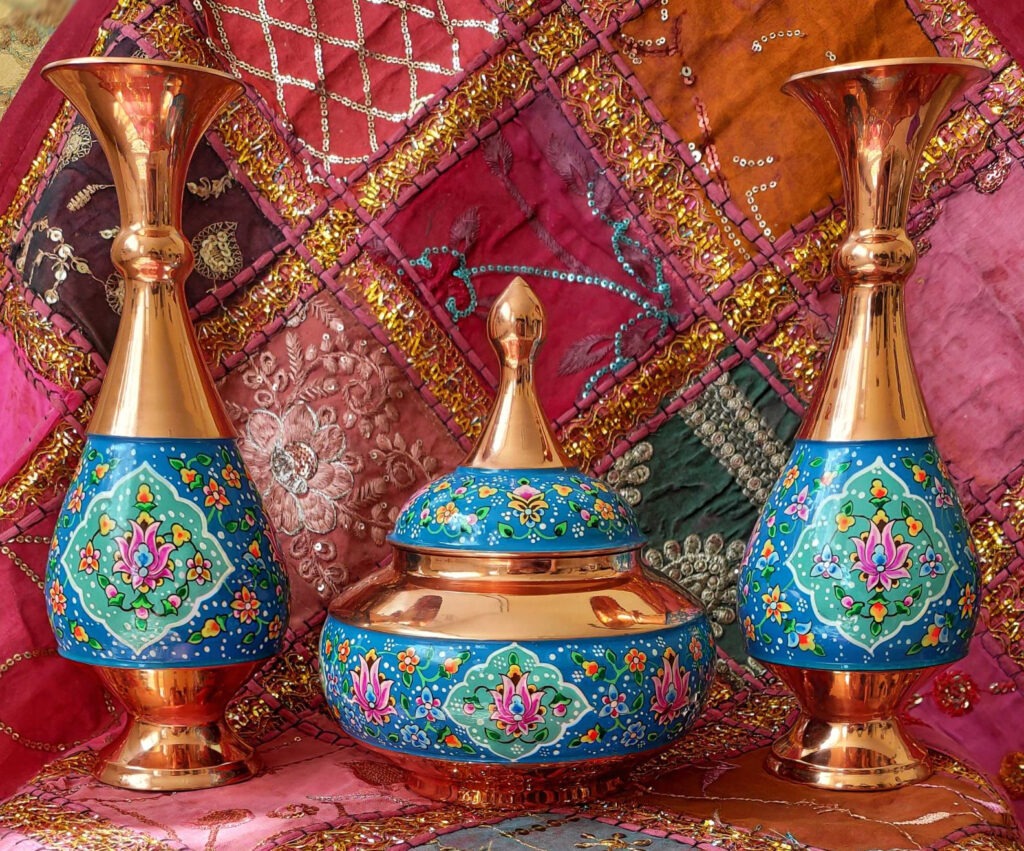
The firing process is both an art and a science—too much heat can distort the design, while insufficient heat may result in dull or uneven coloration.
Once removed from the kiln and cooled, the enamel surface is carefully inspected for imperfections. Even the most skilled artisans may find tiny flaws that need correction. If necessary, additional glazing and touch-up firings are performed to refine the finish.
The final step involves polishing and cleaning the piece to bring out its full luster. Any remaining residues from the firing process are gently removed, and the surface is buffed to perfection. This polishing not only enhances the shine but also ensures that the enamel is smooth to the touch.
A flawless Minakari piece is judged by its rich colors, precise details, and a smooth, glassy finish that reflects light beautifully.
At this stage, the Persian enamel artwork is complete—ready to be displayed, admired, or used as a decorative object. Whether it is a plate, vase, or jewelry piece, each Minakari creation carries the craftsmanship, heritage, and artistic vision of Persian tradition, making it a true masterpiece of enamel artistry.
The Timeless Art of Minakari
Persian enameling, or Minakari, is more than just a decorative technique—it is an ancient artistic tradition that has been passed down through generations, carrying with it the essence of Persian craftsmanship and cultural heritage. The word «Mina» comes from the Persian word for azure or heaven, reflecting the deep, luminous blues that are characteristic of this art form. With its roots dating back to the Achaemenid and Sassanid periods, Minakari has long been a symbol of elegance and refinement, adorning everything from royal artifacts to everyday household objects.
Each Minakari piece is a testament to the artisan’s dedication and the timeless beauty of Persian craftsmanship, ensuring that this exquisite art form will continue to inspire generations to come.
The precision and patience required for Minakari make it one of the most challenging forms of decorative art. Every stage of the process—from preparing the base and outlining the design to applying the black pen, glazing with enamel, and completing the final firing—demands skill, experience, and an unwavering attention to detail. Each step contributes to the final masterpiece, ensuring that the colors remain vivid and the patterns sharp, even after centuries.
Despite its ancient origins, Minakari continues to captivate artisans and collectors worldwide. Today, artists blend traditional techniques with contemporary styles, experimenting with new color combinations and modern interpretations while staying true to the essence of Persian enamelwork. Whether practiced as a cherished hobby or pursued as a professional craft, mastering the five essential steps of Minakari opens the door to a world of artistic expression and cultural appreciation.